3 ways that offer limited success:
- Spray Applied Topical Coatings
- Embedded plastic linings
- Chemical and bacteria additions that alter the production of sulfates and H2S
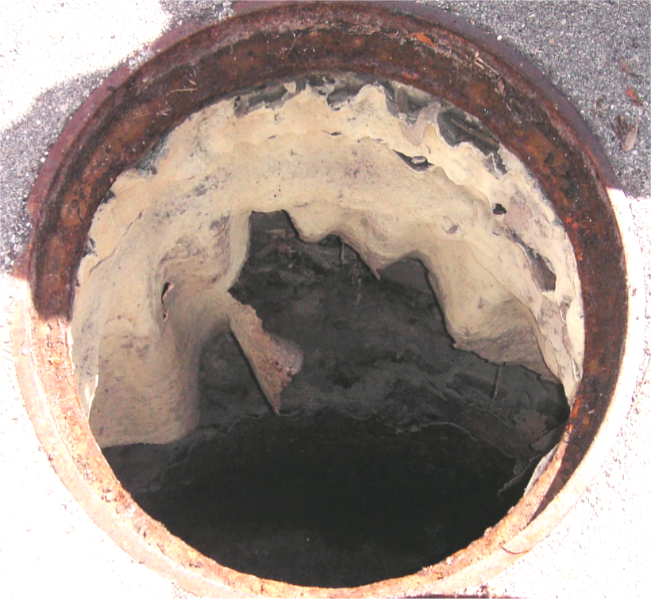
Coatings
There are many types and manufacturers of concrete coatings. The most common are epoxy and urethane based. They rely on adhesion to the concrete substrate to maintain their mechanical integrity. This adhesion is very much disrupted by high alkalinity (such as with young fresh concretes) and moisture. This type of surface treatment is subject to delamination, pin holes / bubbles, scratching, etc. Coatings rely on proper surface preparation and thorough coverage at the prescribed thickness by competent technicians. While in a clean laboratory type of environment it is possible to coat concrete with very good results. In a high capacity modern precast shop or in the field, conditions for a successful coating project are diminished.
Another type of coating is a sodium silicate (water glass) spray. These are often called surface hardeners. They are sprayed on concretes after some initial curing and the silicate ions attempt to link-up with some calcium hydroxide hydrates and form a tough, less permeable surface. This has merit on industrial floors as an example. As discussed above though, MIC is a process by which dilute acids dissolve the lime rich binder matrix. There is little benefit derived from this surface type of treatment.
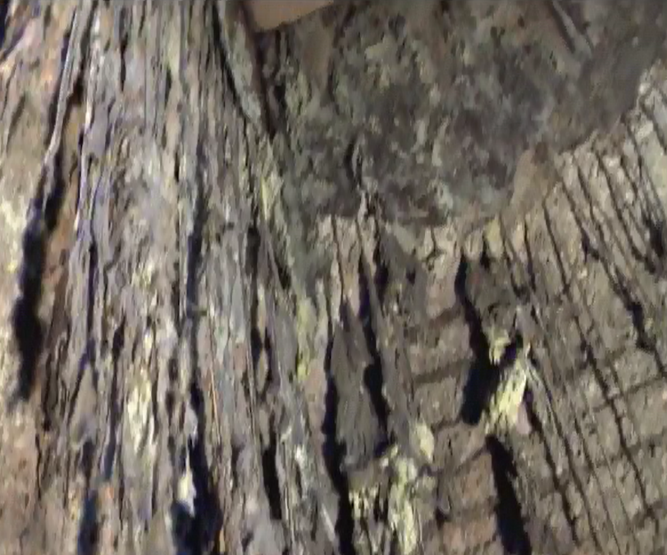
Mechanically Anchored Plastic Liners
These products have been around for many decades and while the liner material itself is very corrosion resistant, the actual installation of the liner remains costly and not without risk. The installation process requires wet casting with relatively high slump concrete mixes. There is the risk of external water pressure penetrating the concrete and causing the liner to bulge and actually rupture. Then there is the issue of welding all the joints and possible damage to the liner during the shipping and installation phase. Welding can only be done by specialty tradesmen which increases cost and usually leads to construction delays. Imperfect welds allow acid to get behind the lining and attack the concrete. The initial cost for a single custom cast in place structure like a pump station is expensive but the implications for mass produced precast shapes like manholes and round pump stations are severe.
Chemical and bacteriological additions to prevent H2S build-up in the sewers
There are three basic ways to control the build-up of hydrogen sulfide in the sewers:
- Prevent its formation in the first place
- Convert it after it has formed but still in solution
- Remove it from the sewer’s atmosphere (both with and without odor control)
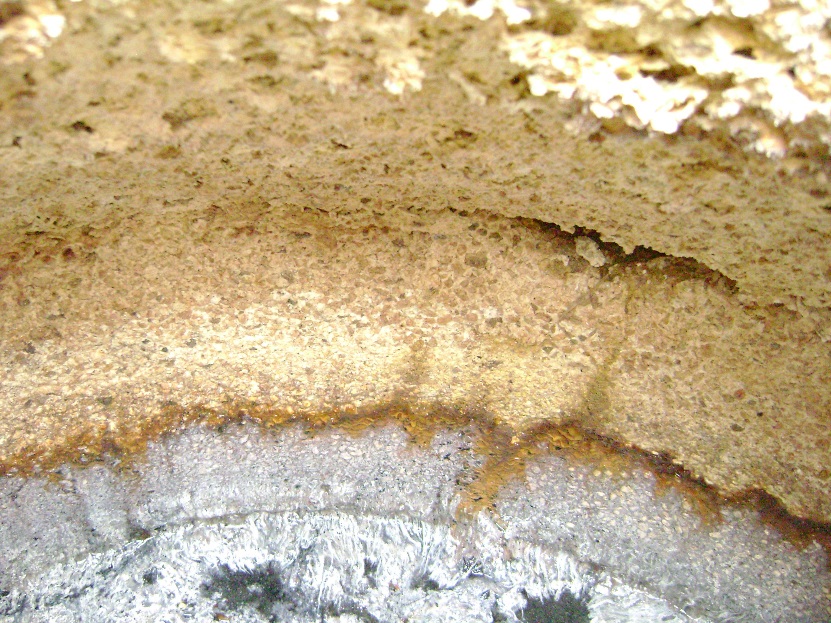
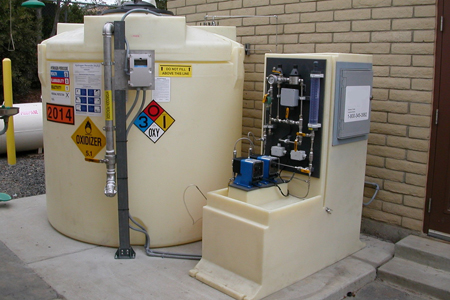
A note on sulphur compounds is offered. In general sulfates are added to the waste water by many avenues. This is a polyatomic anion with the formula SO42-. Once the SRB have acted on the sulfate, three possible forms of sulfides can exist in the water and only one in the atmosphere. In the water the balance is a function of pH. Hydrogen Sulfide (H2S) can exist dissolved in water at high concentrations. In solution, it does not cause an odor or corrosion issue for concrete (metals are another issue.) It will not react with water to form sulphuric acid. Hydrogen Sulfide is the only form which can escape the aqueous solution and exist as a free gas. The other two forms are Bisulfide (HS-) and Sulfide (S=.) Neither can leave the water and do not contribute to color, odor or corrosion issues. H2S is favored at pHs below 7, HS between pHs of 7 to 12 and S at pHs greater than 12.
In general all of the techniques discussed below involve equipment along with varying degrees of supporting infrastructure and consumables. They appear to be used where odor is the driving concern. While these concepts may be feasible at treatment plants, pump stations and other complex structures like large diameter tunnels, how to apply them to a large sprawling collection system is a huge challenge. Odor control is a bit more manageable as structures like manholes can be made somewhat air tight and then the odor issue dealt with at pump stations for example. Corrosion as a result of the increased H2S levels would just get worse in concrete manholes and pipe.
Preventing the reduction of sulfates in the water is theoretically straight forward on a small scale but in a collection system it must be practiced everywhere in a real time fashion. Sodium Hydroxide can be used to increase the pH of the wastewater and in turn inactivate the sulfate reducing bacteria. This has no effect on the sulfides already present. Chlorine Dioxide is now readily available and when used in high dose rates it can destroy the biofilm which contain the sulfate reducing bacteria. It will also oxidize H2S directly with enough time. Sodium Nitrate & Calcium Nitrate retards septicity and promotes the activity of denitrifying bacteria at the expense of the sulfate reducing bacteria. This type of activity can improve the overall operation of the wastewater treatment system. The by-products are various nitrogen containing gases and ultimately just nitrogen. Ozone injection interferes directly with the bacteria cell membranes. It is an unstable gas and must be generated on site. High capital and operational cost remain an issue. Evolving technology involves adding specially developed bacteria that complete with the SRB for available nitrogen and carbonaceous compounds essential for the SRB to thrive.
Once the H2S has formed in solution many chemicals can be added in an attempt to oxidize it. Assuming the liquid waste stream is now rich with H2S still in solution, the idea is to oxidize it back into elemental sulphur or a complex sulfate. The candidates for chemical oxidizers range from ozone, hydrogen peroxide, potassium permanganate, chlorine dioxide, hypochlorus acid, oxygen and various forms of hypochlorite. The preference of one over the other is a complex puzzle of cost, oxidation potential and many other interactions with the complete treatment process. Additionally various iron salts can react with sulfides to form insoluble metal sulfide. Combinations of chemicals are common.
In the third case, H2S gas is in the atmosphere. It can be detected by the human nose in concentrations as low as 0.2 ppm. It has been measured in sewers as high as 1,500 ppm and there are many opinions as to just what level MIC will proceed. It will proceed at any concentration but the rate of corrosion will be strongly affected by the H2S concentrations and many other factors as discussed above. So there is much conflicting data on H2S concentrations and corrosion rates. An older common idea was to flush the H2S just with large volumes of air. Odor quickly becomes a problem. Often times the air was introduced in the water in an attempt to purge as much of the H2S as was possible. Odor controlling air scrubbers have been employed and they have significant issues with space, capital cost, consumables, etc. A common idea is to ensure that only aerobic conditions exist in the liquid phase. Many variations on the theme have been tried. The solubility of oxygen or air in water is very low and so the dosing would have to very low and at frequent locations. Proper process control is difficult and odor and corrosion problems are sometimes made worse.