Much has been written incorrectly on just how concrete is destroyed by MIC but in fact the action is very simple. How the acid is produced (covered above) is the only phenomena. Most economical cementitious concretes and mortars are bonded with hydraulic cements that are rich in calcium oxide. It does not matter what type of Portland or calcium aluminate cement is employed as the binder. New so called geopolymers are hindered as well. In order to produce economical binders that can develop strength under normal curing conditions lime containing raw materials (fly ashes and Portland cement) are required. Alkalies of sodium are used to activate the condensation process. The end result is that the basic minerals and the resulting hydrates (or condensates) are simply very soluble in the dilute acids. This type of corrosion is dominated by the weakest material in the matrix. This is not an averaging situation and there is no passivation caused by the corrosion bi-products as with some metals. What is left behind is a crumbly mass of aggregates and calcium sulfate based complexes.
The use of sacrificial (limestone based) aggregates has proven to not be a long term effective solution in such areas as south Florida where these are generally the most economical aggregates. This will be discussed further.
Again despite many published articles, Portland cement based concretes will be attacked by dilute acids at any pH below 7. Below a pH of 5 the problem becomes acute and below a pH of 4 corrosion rates of 1 inch per year can be expected. Furthermore, the problem accelerates as the surface pH continues to lower where the bacteria thrive even more. Concrete test specimens in the states of Florida, Texas, Washington, Indiana, etc. have had pH values drop to near 1 in less than 3 years.
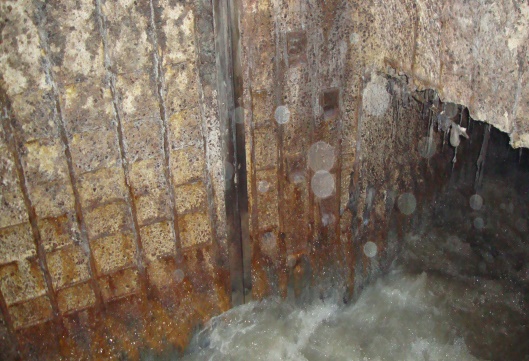
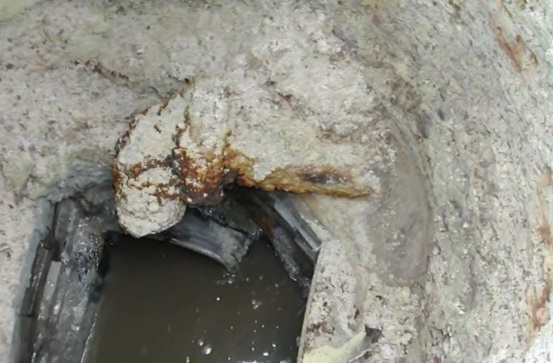
BASIC CEMENT CHEMISTRY
A quick review of hydraulic cements suitable for mass produced concretes shows that all are rich in calcium oxide. First, their stoichiometric chemistry at the time of production is constrained by 3 factors:
- The source of lime and silica based raw materials
- Economical production
- A limited range of chemistry that will hydrate
By far the most universal cement in the world is Ordinary Portland Cement (OPC.) It is rich in calcium oxide (also known as lime – CaO or just C in cement chemistry notation.) Much of the lime in OPC is contained in two minerals containing silica (silicon dioxide – SiO2 or just S.) These precise minerals form in the rotary kiln at ~ 2,600 to 2,800°F under sintering conditions.
These minerals are:
- Alite or Ca3SiO5 or just C3S – accounting for ~ 40 to 70% of the cement
- Belite or C2S – accounting for ~ 15 to 25% of the cement
The raw materials (one rich in calcium compounds and the other rich in silica compounds) used in the production process contain impurities such as compounds of iron (F,) alumina (A) and alkalies. These combine in many complex ways during the sintering process but mainly form C3A and C4AF. During grinding of the sintered clinker, calcium sulfate is added to control the flash setting C3A. The Alite and Belite ultimately provide most of the strength development and also establish the hardened cement’s reactivity to various chemicals such as acids. To demonstrate the limited ways in which to manufacture cement, the 3 component phase diagram for Lime – Alumina and Silica is shown at the end of the paper (figure 1.) The minerals in question can be seen in the small blue oval along the left most axis of the triangle. Adding a fourth component such as iron oxides requires a three dimensional model and adds greatly to the complexity of the system. Add still again various alkalies and the picture becomes something that cement chemists spend their entire careers studying with results often times limited to a particular plant and its available raw materials. As can be seen, there is a very limited ratio of raw materials that can form practical cements.
Unfortunately this is not the exact chemistry needed to produce a perfect hydrate structure. Highly permeable / soluble crystals, gels and watery voids result for considerable periods of time. The calcium rich hydratable minerals that can be produced are simply too rich in lime ultimately. Just a few of the basic calcium and calcium silicate reactions are shown in figure 1 but again they dominate the Portland cements hydrate system and establish the limitations on its chemical resistance.
The C-S-H hydrates do not have a set chemistry or a firm crystalline structure but are an amorphous gel with a combination of varying hydrates and watery pores. The watery pore space is a defect in the structure but is necessary for the hydration to have space to develop. As much as half the water indicated in the equations may be in the pore space. Hence the confusing notion that OPC only requires ~ 20% water for complete hydration. Hydration would stop at some point with a water level this low. As mentioned above though, the watery pore space is a defect in the hardened structure and the best mechanical properties and resistance to penetrating ions are achieved with a compromise of water additions.
To the extreme right side of the chemical reactions, are the simple calcium hydroxide (CH) hydrates. These minerals do have a pronounced crystalline structure forming early in hydration.
Within the complex C-S-H gel system there can be many different imprecise combinations of atoms. The silica component in particular may be attached to anywhere from 2 to 3 to 4 oxygen atoms as an example. There may be some crystal structures but in general the gel is amorphous. Two of these crystalline minerals can be; tobermorite (~ C6S5H9) and jennite (~C9S6H11) both allowing for the formation of even more CH as the C to S ratio drops. These minerals may become more prevalent over long periods. The single most important point to be stressed is that the binder phase is dominated by calcium based minerals.
HOW ARE CEMENTS & CONCRETES DEGRADED BY NON-MECHANICAL MEANS
Acid attack is one where the surface is systematically dissolved and exposes the next layer to fresh acid. Think of it as liquid chemical erosion. Everyone can imagine plate glass is very impermeable. Pouring certain acids (such as Hydrofluoric acid) on it can etch it – or to use another term – corrode it. It is clear this is a surface phenomenon – the acid does not penetrate the glass. In the case of MIC the deterioration produces a number of non-binding mineral by-products. For this reason, attempts to make concrete less permeable have provided little improvement in long term chemical resistance. Likewise attempts to further combine the available calcium oxide in Portland cements with pozzolanic (that is material high in reactive silica like fly ash and fume silica) materials have proven ineffective. Short term strong acidic liquid emersion tests provide little insight as to the long term performance of a cementitious specimen in dilute acids. A recent presentation on geopolymers claimed complete protection from MIC as a short term test in 7% sulphuric acid showed only a 10% mass loss in 84 days.
When converted to single sided corrosion rates, the loss is ~ 1/16” in 84 days or 3 inches in 10 years. Many confuse sulfate attack (from hot soils and seawater where permeability reductions can help a great deal) with acidic corrosion in sewers.
First the distinction must be made concerning a surface attack by acids versus an internal attack caused by penetrating ions or freeze / thaw. Also in some cases it is not the cement that is directly attacked but the concrete system as a whole.
A perfect example is penetration of chloride ions from both seawater and de-icing salts. Portland cements are not especially attacked by these ions but the ions are very mobile though the watery pore space of the hydrated cement system. These mobile ions reach the reinforcing steel which was initially well pacified by the high pH of the surrounding concrete. A very thin and tough oxide layer is formed early on during hydration. The exact mechanism of chloride ion attack is somewhat unclear but the general consensus is that the chlorides mainly serve to break down the oxide layer and allow for a natural half-cell oxidation reaction in which electrons flow from anode to cathode sites. There, a reduction reaction takes place with water and oxygen combining with the free electrons forming OH radicals. They quickly combine with the iron and form iron hydroxides or rust. The steel is not only reduced in strength but the resulting rust production is very expansive and causes the surrounding concrete to heave and disbond from the steel. There can be a second reaction in which the chlorides combine with the iron and form iron chloride as an intermediate step. This product combines with water under reduced pH and iron hydroxide is produced along with hydrochloric acid (HCl.) The pH drops radically and the corrosion process is accelerated.
Another example is sulfates from either highly sulfated soils or seawater. Again these sulfate ions are very mobile. They do not directly attack good strong calcium silicate hydrates but they have an affinity for the Tricalcium Aluminate complexes and calcium hydroxides found in Portland cement. The resulting reaction produces a powerful expansive formation of the mineral ettringite, a large high water calcium sulphoaluminate (CSA) mineral. This attack is found on the outside of concrete pipe and structures, inside septic tanks where waters are high in sulfates, etc. (Not to be confused, this mineral may also appear as the result of MIC but it is an after affect – not the cause of concrete attack.)
Damage to concretes caused by freezing and thawing is another internal issue but is caused by the relatively large amount of water in the watery pore space in the hydrate system. The freezing and thawing of the water causes repeated expansion and relaxing of the cement matrix and it ultimately fractures.
Chemical attack by dilute acids such as hydrochloric or sulphuric or nitric acid, etc. is purely a surface attack. Any penetration of the surface is academic as the bulk of the damage is the simple result of the various hydration products being dissolved in the aqueous solution of acid. This is analogous to corrosion of dense metals by acids. The attack is on the surface and just works through the fresh unreacted material over time. The table below shows how some various acids react with the calcium hydroxide portion of cement hydrates and dissolve them leaving behind water and salts.
Type of Acid | Lime + Acid | Result | Salt + Water |
Hydrochloric | Ca(OH)2 + 2HCl (aq) | CaCl2 (aq) + 2H2O | |
Phosphoric | 3Ca(OH)2 + 2H3PO4 (aq) | Ca3(PO4)2 (s) + 6H2O | |
Sulfuric | Ca(OH)2 + H2SO4 (aq) | CaSO4 + 2H2O (gypsum) |
A BASIC REVIEW OF SOME INORGANIC CHEMISTRY
As a review, there are very few elements found naturally in nature in a pure form. Gold, platinum and occasionally sulphur can be found. Most metal elements are very reactive chemically and are found only as oxides and then in complex minerals containing several different oxides. One relatively pure metal oxide found in nature is crystalline silica sand and some silica rocks (both crystalline and amorphous ones.)
Most pure (highly processed) metals are quickly consumed by acids including; aluminum, calcium, chromium, nickel, copper, iron, etc. There are only a few exotic metals that are resistant to acids. But in certain cases, a pure metal oxide can be extremely resistant to certain strong acids such as alumina (AL2O3) and silica (SiO2.) Some alumina silicate minerals are very resistant to certain strong acids. Other oxides are quickly consumed by acids such as Iron Oxide (both FeO and Fe2O3) and most importantly Calcium Oxide (CaO.)
Generally complex minerals (whether naturally or synthetically formed) are prone to consumption by acids when at least one component has weak resistance to acid. Hence a complex calcium silicate or calcium aluminate, etc. will be quickly consumed by acids even though one component appears to be resistant. In hydraulic binders such as Portland cement the addition of water molecules to the mineral to form a hydrate has no improved resistance to acids. The overall durability is a like a chain – it is no stronger than the weakest link – the calcium oxide. In the case of concretes, there is no averaging of the affects and there is no passivation caused by the corrosion bi-products as with some metals. What is left behind is a crumbly mass of aggregates and calcium sulfate based complexes with no structural value.
Again despite many published articles, Portland cement based concretes will be attacked at any pH below 7. Below a pH of 5 the problem becomes acute and below a pH of 4 corrosion rates of 1 inch per year can be expected. Furthermore, the problem accelerates as the surface pH continues to lower where the bacteria thrive even more.