Typical Ordinary Portland Cements or (OPC):
There are 5 general types of Portland cement. There are also many special varieties covered by ASTM standards such as those for masonry work, white Portlands, several oil field grades, blended cements and expansive cements. The 6 most common are summarized below:
- Type I – typical Portland
- Type II – a moderate sulfate resisting cement
- Type I / II a cement that provides the strength gain requirement of Type I but with chemistry meeting Type II specifications
- Type III – high early
- Type IV – low heat for mass concreting
- Type V – more sulfate resisting
Generally cements richer in Alite (C3S) produce higher early strengths and more heat is liberated. Improved sulfate resistance is achieved by lowering the C3A content. As an example, Type III would be relatively higher in C3S and C3A and be ground finer. This would be a very bad choice for a concrete subjected to sea water or highly sulfated soils.
In the case of direct surface chemical attack by dilute acids, none of the above Portlands would be any better than the other. This is a common mistake where sulfate resisting is taken to mean sulfuric acid resisting.
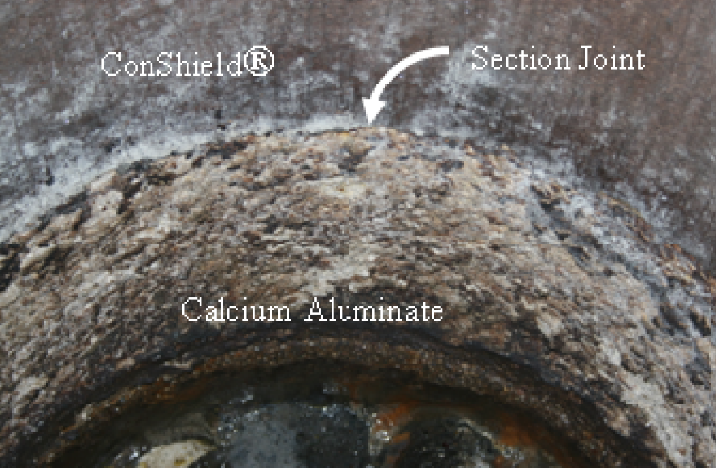
Other types of cements:
Calcium Aluminates:
So it would seem that traditional Portland cements need to be improved or replaced. This is not a new concept and the giants of the cement industry have been studying this problem for more than 120 years. Calcium Aluminate Cements were first envisioned in the late 1890s and Lafarge pursued production in the early 1900s. This cement was developed for improved protection from sulfates – not sulphuric acid or any other strong inorganic / organic acid. This special class of cement went on to have a number of important uses outside typical structural concretes. Its effectiveness against sulfate attack was later made uneconomical by the development of Type II and Type V Portlands and the use of pozzolans and water reducing admixtures. Calcium Aluminates produce alumina gels and calcium aluminate hydrates, that while better than typical Portland cements (from a general corrosion point of view,) they cannot survive the attack of the powerful acids ultimately produced in certain sanitary sewers. These are conditions where the pH of the dilute acids reaches well below 3 and even less than 1. Here any calcium oxide based hydrate structure is going to be destroyed in short order. Studies conducted by the University in Hamburg show the improved performance of calcium aluminate cement based mortars for a while but then the corrosion process ultimately gains momentum.
Ground Blast Furnace Slag (GBFS):
Various claims for ground blast furnace slag cement and Portlands interground with slags and limestones still result in a rich calcium oxide based hydrate structure. Iron making (not to be confused with steel making) results in a large quantity of slag floating to the surface in a blast furnace or cupola. The slag is based on limestone (with the CO2 driven off) and the chemistry is such that the impurities in the iron ore (rich in silica and alumina) react with the calcium oxide and form a high melting light (that is how it floats on the molten iron bath) slag. The slag is tapped from the furnace before every iron tapping event and when it cools (solidifies) it can be ground in large ball mills typical of those in the cement industry. These slags can have a high degree of the same calcium silicate and calcium aluminate minerals found in OPC. Slags vary from plant to plant and day to day as the iron process is first and foremost controlled to produce high quality iron that is fed to the Basic Oxygen Furnaces (BOF or the steel converter.) Steel slag is not suitable for use in concretes. In the past there were experiments suggesting a corrosion resistant binder could be produced in the form of a supersulfated slag. Like many things it is an improvement upon OPC but in a narrow field and is not completely effective. A lime rich binder still dominates the corrosion issue.
Alkali-Activated Alumina Silicates or so called Geopolymers:
For many decades, cement technologist have chased the concepts of activating silicas and alumina silicates directly to form some type of binding structure. Using some highly refined minerals and chemical additives it is possible to develop in the laboratory some remarkable products. Generally high temperatures or autoclaving are needed to drive the reactions. In the high temperature hot metal industries like iron & steel, castable refractories are consumed which feature essentially no lime. These materials are very temperamental and cost several thousand dollars per cubic yard just for raw materials. They have poor green strength. For typical infrastructure construction / repair, only economical binders are feasible. So the typical geopolymers offered today are based on waste products like fly ash. In order to produce controlled setting times and early strength gain (similar to OPC) these products need strong additions of alkalies and lime (from within the fly ash or from OPC.) Water requirement is generally lower for geopolymers and does not become part of the hardened binder. The water is there to serve as a medium in which the various reactions take place, namely the initial disassociation of ions followed by the condensation of the actual binding phase. Recent corrosion claims for geopolymer cements based on fly ash have the same Achilles heel as OPC – namely the lime content. The graph below shows a geopolymer performing much better than a simple Portland cement based mortar. However, corrosion becomes severe after ~ 40 days. When converted to a single sided model, the corrosion rate suggests a loss of material over 3” in 10 years. This is not trivial. To further compound the story, this particular material was post treated with a sodium silicate solution. This is old technology used to harden the surface of industrial floors. It is well known to only offer a short term improvement in chemical resistance. Another issue is the long term durability of these binders. Little experience exists and most testing is performed using long ago developed standards for OPC and typical concretes. These standards have been verified by many years of real world experience. Whether they are applicable for geopolymers remains to be determined. There are no ASTM standards for these materials nor are any such products offered today by the leading cement manufacturers.